Keimyung University: Researchers Explore FDM 3D Printing in Feasibility of Manufacturing 3D Printed Medications
Researchers from Keimyung University have published a recent article exploring how new processes may change the realm of pharmaceuticals in ‘Complex formulations, simple techniques: Can 3D printing technology be the Midas touch in pharmaceutical industry?’ The authors are well aware of the typical benefits of 3D printing such as affordability, speed in production, and the potential for cutting out labor and on-site factory expenses; however, the benefits in pharmaceuticals extend far beyond the basics due to the ability to make medications that are personalized, with patient-specific dosages that could be made in a variety of different forms—and released into the body at varying levels of intensity.
The researchers address varying types of 3D printing technology being used currently in pharmaceuticals, and their focus for the study at hand:
“Various technologies such as fused deposition modeling (FDM), selective laser sintering (SLS), stereolithography (SLA) and inkjet or binder jet printing (IJP), have been studied for the development of different formulations and have been described in this review,” state the researchers. “However, most of the studies have been carried out using FDM and inkjet printing, which are considered the simplest and most feasible methods for the formulation of dosage forms using 3D technology. Hence, in this review, special attention has been paid on the principles and studies done using FDM and ink-based printing technology as well as the challenges faced by 3D printing in the pharmaceutical sector.”
FDM 3D printing has been known for challenges in loading drugs into different types of filament, along with releasing of medications, but the scientists are still optimistic:
“These studies show that even with FDM there is a possibility of expanding the scope of 3D printing together with a wide range of excipients and APIs.”
Some of the promise behind FDM 3D printing in pharmaceuticals may be due to the amount of accuracy and versatility available, along with the ability for users to employ multiple nozzles. The researchers state that this is a major break-through with the possibility of making variations such as coated tablets that would require dual nozzle capability. Previously, variety in shapes and forms of tablets has caused erratic performance in drug delivery, along with the issue of APIs as one of the major stumbling blocks due to chemical incompatibility.
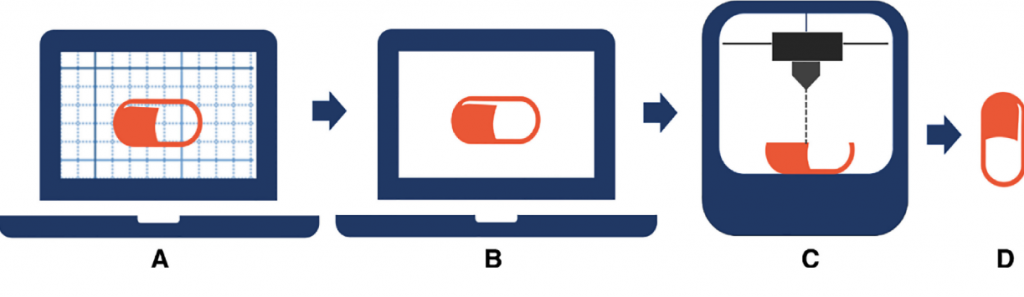
General process of 3D printing with reference to nozzle-based printing: Design of the object using computer aided design software (CAD) and file saved in STL. (A) format Slicing and printer setting using slicing software; (B) file saved in format supported by the printer (e.g. G-code); (C) printing of designed object using suitable 3D printing technology (e.g nozzle-based technology); (D) finished printed object.
“One of the solutions to this problem is a bilayer tablet with different formulation blends to modify the release and to separate the APIs,” state the scientists.
It is also hoped that 3D printing may be able to precipitate greater usage of capsules in patient-specific medications, due to the possibility of offering a single-step process. A process has also been created for making liquid medications via FDM 3D printing with a syringe nozzle. Another method in FDM 3D printing was tested using ibuprofen for ‘sustained release,’ along with other tablets made of predesigned scaffold structures. Fast-dissolving film (FDF) medications show promise too.
“Formulations by FDM provides good mechanical strength and high resolution, but the used thermoplastic material should be suitable for extrusion and infill percentage of drug should be optimized to obtain the desired release profile. FDM has been most commonly discussed as the best technology for medicine printing and it can also formulate very complex geometrical dosage forms, which was not feasible with conventional manufacturing process. FDM technology surely opens a new revelation in personalized medicine,” concluded the research team.
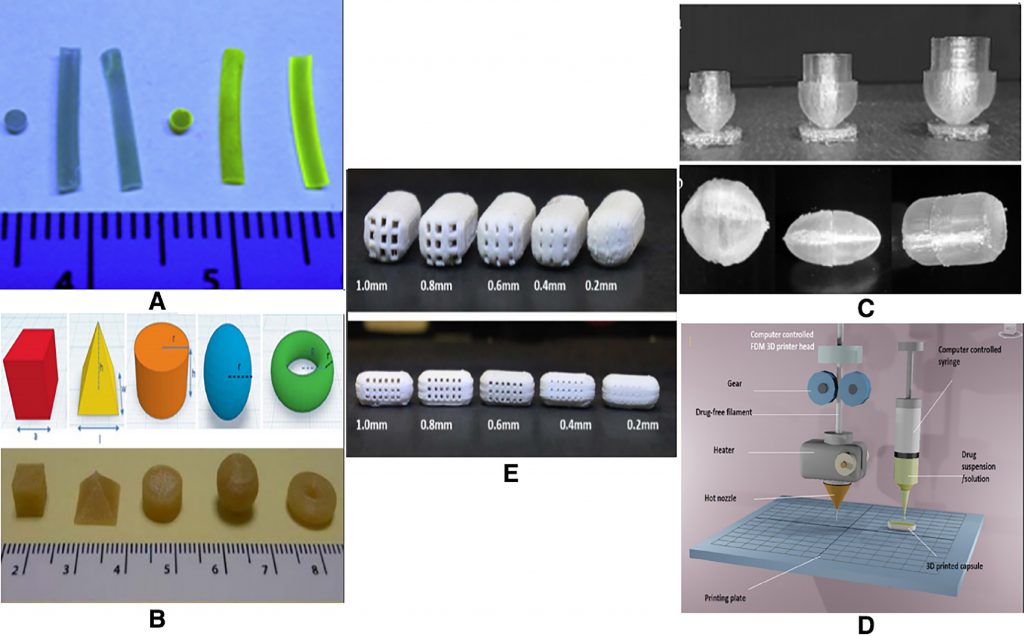
Examples of applications of 3D printing in pharmaceutical sector. (A) Images of PVA filament (left) and fluorescein-loaded filament (right) under UV light (Reproduced with permission from [11]. Copyright 2014 Elsevier B.V.); (B) Design and printed tablets of different geometrical shapes using FDM technology (Reproduced with permission from [43]. Copyright 2015 Elsevier B.V.); (C) Multicompartment capsular device printed using FDM technology (Reproduced with permission from [48]. Copyright 2015 Elsevier B.V.); (D) Dual-nozzle FDM (Reproduced with permission from [50]. Copyright 2018 Elsevier B.V.); (E) Channeled tablets (front and side view with channel sizes) (Reproduced with permission from [57]. Copyright 2017 Elsevier B.V.).
What do you think of this news? Let us know your thoughts! Join the discussion of this and other 3D printing topics at 3DPrintBoard.com.
[Source / Images: Complex formulations, simple techniques: Can 3D printing technology be the Midas touch in pharmaceutical industry?]
Subscribe to Our Email Newsletter
Stay up-to-date on all the latest news from the 3D printing industry and receive information and offers from third party vendors.
Print Services
Upload your 3D Models and get them printed quickly and efficiently.
You May Also Like
3D Printing News Briefs, August 16, 2025: European Distribution, Expeditionary Powder, & More
We’re taking care of business first today in 3D Printing News Briefs, with Wayland Additive appointing a new Chief Technology Officer and AML3D expanding its European distribution. Moving on, Metal...
3D Printing Financials: Velo3D Grows Revenue in Q2, Targets 2026 EBITDA Breakeven
Velo3D‘s (OTCQX: VLDXD) latest earnings show that the company is continuing to recover momentum after a rocky 2024. In the second quarter of 2025, the metal 3D printing company posted...
3D Printing Financials: Xometry Sets New Record in Q2
Xometry (Nasdaq: XMTR) has reported its best-ever quarterly results, with strong growth across its online manufacturing marketplace. The company saw gains in revenue, profit margins, and customer activity, pointing to...
3D Printing News Briefs, July 31, 2025: Falcon A1 Pro Launch, Kickstarter 3D Printer, & More
Today’s 3D Printing News Briefs is all about new products! We’ll tell you about some new components and machines related to additive, as well as a new 3D printer on...